What is the Difference Between Compliance and Conformance?
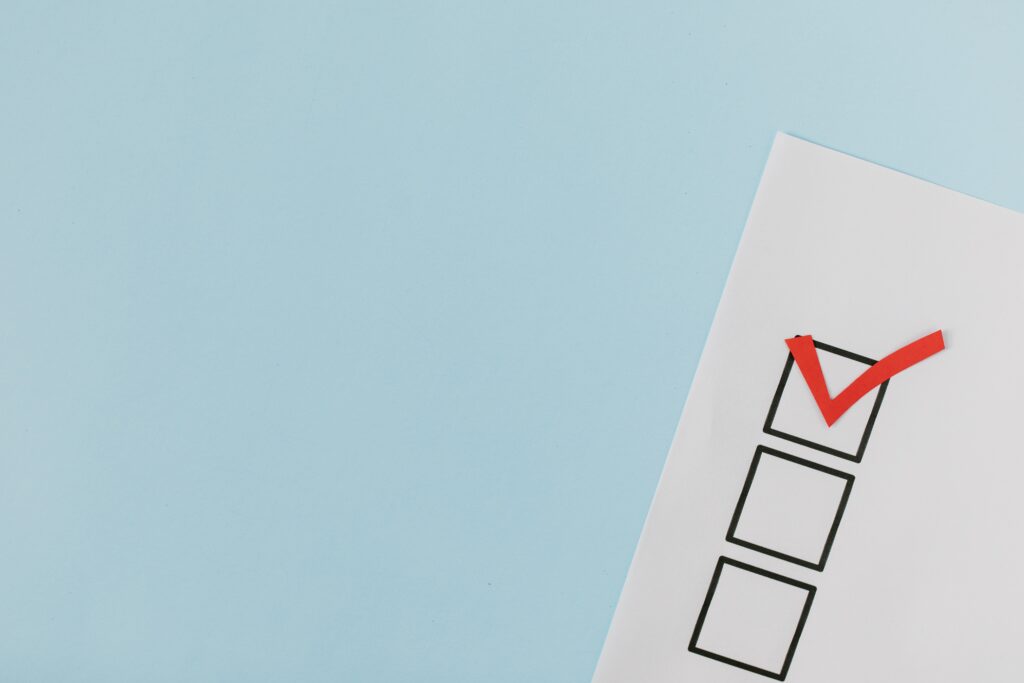
Introduction
Virtually every company, regardless of the industry, conducts its activities under set standards, guidelines, and regulations. In some cases, these guidelines detail internal procedures that must be adhered to in order to ensure the company’s product/services keeps meeting the standards considered satisfactory to the consumer. In other cases, these guidelines are prescribed the external regulatory bodies and deviations come with strict penalties. The distinction between internal and external standards creates the need to differentiate between compliance and conformance.
Comparing Compliance and Conformance in Quality Management
Compliance and conformance are two critical aspects of quality management. Although both terms are often used interchangeably, there is a clear distinction between both, and using one in place of the other will be technically incorrect.
In general terms, compliance deals with the regulatory or legal requirements a company’s products or services must meet before they are certified okay to market. These guidelines are often set by regulatory bodies and a failure to strictly adhere to these requirements could have serious legal implications.
For example, a company producing food products must comply with the relevant food safety laws before it can release the products to consumers. These laws may be formulated by the local or state authorities or even the FDA, and they’ll typically detail how the company is expected to source raw materials, handle and store them and prepare their products.
The company’s quality management team would be responsible for checking and verifying that these standards are being met and the results must be documented appropriately. Deviations from these standards present compliance challenges and they may be detected either internally or by external auditors.
On the other hand, conformance deals with customer or industry-specific requirements products need to meet before products are released to customers. Conformance guidelines are typically established by the company itself or some other governing body that stipulates industry-specific standards.
For example, the company above may belong to a national food processing association with guidelines for the minimum quality standards companies’ products must meet before they’re certified okay by the association. Alternatively, the company may additionally have internal standards for ascertaining the quality of raw materials or final products. Deviations from these regulations are known as nonconformance, and they’re typically detected by the internal audit team or by the audit team of the body responsible for the certification. For more context, ISO is the body responsible for setting conformance standards in many industries.
In summary, Compliance is what the law requires of the company while conformance is what the company commits itself to.
Are there any similarities between compliance and conformance?
In many cases, the programs and certifications that fall under compliance and conformance requirements may feel quite similar. Both certifications also require impeccable record-keeping and frequent random audits. However, the main difference is that compliance is mandatory while conformance is voluntary.
Thus, if a company runs afoul of conformance requirements, the ultimate punishment is that it will lose its certification. However, breaching compliance guidelines will come with stricter penalties.
Interestingly, many industries have conformance systems that run parallel to compliance systems. So, if the company voluntarily subscribes to such conformance systems, it’ll have little trouble with compliance.
A typical example is comparing ISO 13485 for Medical Device Manufacturing with 21 CFR, part: 820. While the former is a voluntary conformance requirement, the latter highlights mandatory requirements that medical device manufacturers must meet. However, any company that meets the standards of ISO 13485 will have little trouble meeting the requirements of CFR 21. And since ISO audits are more frequent, most companies strive to maintain the certification since it makes passing FDA audits much easier.
Curiously, many organizations that do not even produce medical devices but manufacture parts for medical devices manufacturing companies also strive to maintain ISO 13485 certification. This is because the certification can significantly increase the quality of their output and also aids trust between the company and their target audience (medical device manufacturers). This is a classic example of how conformance can be the distinguishing factor between companies doing the bare minimum and those doing their utmost to ensure customer satisfaction.
Why is Compliance Important?
There is no over-emphasizing that following the regulations, specifications, and standards set by regulatory bodies is essential to the growth and continued existence of any organization. Below are some of the consequences of non-compliance:
- Legal and regulatory concerns: Non-compliance with regulatory guidelines can lead to sanctions, fines, and other penalties. The severity of the punishment will depend on the nature and extent of the violation. And in some cases, the company may have to deal with lawsuits and class actions, alongside government penalties.
- Reputation damage: Non-compliance casts a bad light on the company’s reputation, and the consequences can be far-reaching, especially if the knowledge becomes public. Existing customers would lose trust in the company’s product or services and the company would find it difficult to attract new ones.
- Product recalls: Non-compliance may lead to costly product recalls. Beyond the financial implications, the company would also need to invest hugely in customer compensation and reputation management. Little wonder organizations without adequate financial muscle typically struggle to recover from major non-compliance issues.
- Reduced productivity and efficiency: Some non-compliance issues require additional time and resources to resolve. Ultimately, this can affect the company’s production chain, alter delivery times, and generally lead to reduced efficiency.
What are the consequences of non-conformance?
Just like non-compliance, non-conformance also poses serious threats to a company’s reputation and image. The distinction is that while non-compliance would certainly lead to legal penalties, it’s still easier to get away with non-conformance. However, the potential consequences are just as serious, and here are a few of them:
- Reduced customer satisfaction: Since most conformance regulations are put in place to ensure a high-quality output, non-conformance is likely to result in reduced customer satisfaction. This would in turn result in lower customer loyalty, negative word-of-mouth reviews, and overall damage to the company’s reputation.
- Increased risk of product defects: Although some non-conformance challenges may seem innocuous, they actually lead to an increased risk of product defects and safety hazards. When left unaddressed, the company may be exposing its employees and customers to harm and this would affect its reputation.
- Increased production cost: Solving non-conformance challenges may entail product recalls, rework, scrap, or some other approach depending on the nature and severity of the challenge. These approaches are often costly to implement and they even disrupt the regular flow of work in the company.
- Loss of certification: Some non-conformance cases automatically result in a loss of certification by the relevant body. This can be devastating to the company’s reputation, especially in industries where potential customers seek out companies with these certifications. Such a company would struggle to compete with other players in the industry until the certification is regained.
How to Identify Compliance and Conformance Challenges
Identifying and resolving compliance and conformance challenges early is crucial to minimizing the potentially devastating consequences of non-compliance and non-conformance. However, this can only be achieved by companies that employ an all-encompassing approach to quality management in general. Below are a few steps companies can put in place to facilitate early detection of compliance and conformance challenges:
- Review relevant guidelines and regulations: Reviewing the relevant guidelines and regulations is the first step in identifying compliance and conformance challenges. A comprehensive review helps to identify the shortcomings in your current quality management strategies while making it easier to come up with improvements. The reviews may come as process audits, employee interviews, or analyzing available data to identify trends that are suggestive of non-compliance or non-conformance.
- Analyze customer feedback: One of the most important indicators of non-conformance is consistent negative customer feedback. Customer feedback helps identify areas where the company is falling short of customer requirements or expectations. If the negative feedback is traceable to compliance and conformance challenges, the relevant team can take the necessary action.
- Schedule periodic internal audits: Regular audits provide a great avenue to review internal procedures and identify existing compliance or conformance gaps. The audits should cross across all relevant departments, including but not limited to, operational, logistics, manufacturing, technology, and regulatory. It is vital that the auditor remains independent when reviewing the company’s operations and processes and implementing the necessary auditing standards. If this can be done, the chances of failing external audits become minimal and the company can guarantee their customers will continually enjoy high-quality products and services.
- Use the right software: Software has become an integral part of quality management, and if you are not yet on the train, it is time you jump on. Companies with the right compliance and conformance software greatly minimize the risk of human errors while ensuring that their processes continue to measure up to internal and external standards. Additionally, the right software ensures all aspects of conformance and compliance testing are covered, from documentation to process audits to reporting and everything in between.
What to Look out for in the Right Compliance and Conformance Management Software
As earlier mentioned, the right software is essential to overcoming common compliance and conformance challenges. But how do process owners identify the right software for their organization? Here, we share a few tips you will find useful:
- Quality Management Suite: Compliance and conformance detection are typically built into a company’s overall quality management strategy. This approach is effective because it facilitates the early detection of challenges while ensuring all relevant departments have access to the needed data. Thus, any software you are considering should come as a quality management suite with other capabilities such as audit management, Corrective/Preventive Action (CAPA) Management, Document Control, etc.
- Enterprise Specialization: Some compliance/conformance management systems are designed for specific industries such as healthcare, IT, food, etc. Before choosing such a system, you should be sure that it offers the solutions you need. Better still, you can choose a system that is flexible enough to offer compliance management solutions for a wide range of sectors.
- Comprehensive Documentation and Reporting Capabilities: Remember, one of the reasons why you are going digital with conformance/compliance management is to eliminate the potential errors that come with manual documentation and reporting. Thus, your software of choice should deliver comprehensive reporting that would capture all relevant details. Importantly, the software should also possess excellent document version control capabilities. This ensures that you have access to all relevant documents at all times.
- Simple and User-Friendly Interface: Although often overlooked, the user interface is a key component of any quality management system. Employees often struggle with complex systems and this may affect the quality of input, and consequently, the results generated. Your best bet is to choose software with an intuitive and user-friendly interface as well as functions that can be easily understood by all team members.
- Multi-level Workflow: It’s vital to understand that many compliance and conformance review processes are not linear. More often than not, different departmental managers need to append their approval and a conformance management system with multi-level workflow capabilities can take charge of the entire process. Such a system would understand that the process can only be marked complete after necessary approval from all relevant departments. In cases where a department is delaying the workflow process, the system will send reminders to ensure the job is done.
Enjoy the Trackmedium QMS Advantage
If you need conformance and compliance management software that ticks all the relevant boxes, Trackmedium QMS should be the first name on your mind. The software comes as a quality management suite that allows companies to automate regulatory compliance and quality management across all aspects of their production and supply chain. Quality managers who rely on Trackmedium QMS can guarantee better and safer products for their consumers while ensuring that the company detects production problems that can lead to expensive recalls and loss of consumers’ trust early enough. Reach out today to learn more about how you can gain a competitive advantage with Trackmedium QMS.