Why is Non-Conformance Management Important?
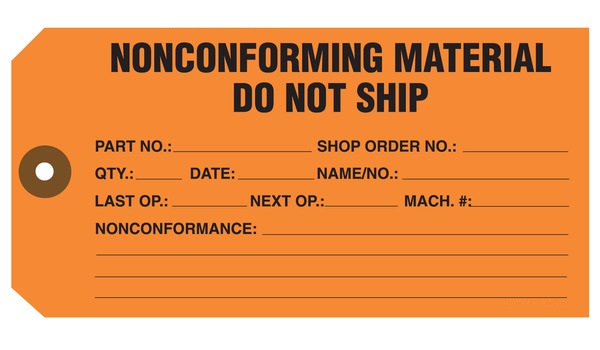
Non-conformance management refers to the process or guidelines involved in identifying, documenting, and addressing issues pertaining to non-conformance. This process is crucial to minimizing the impact of non-conformances on an organization’s operational output, reputation, and by extension, customer health. FDA-regulated industries, such as medical devices, life sciences, and pharmaceuticals are especially prone to non-conformance incidents. As such, many organizations in the industry often add the “cost of conformance” as part of their operating costs.
A robust non-conformance management system ensures that non-conformances are promptly identified and addressed in compliance with regulatory standards. It is an essential part of any quality management system, and it helps organizations improve the quality of their product and services, and minimize errors that can affect the cost of production while staying on the right side of the law.
Benefits of having a robust non-conformance management system
Apart from obvious regulatory concerns, leaving non-conformances unchecked poses a threat to the continued existence of any organization. Below are a few benefits of having a robust non-conformance management system:
- Improved quality
Non-conformances are essentially product or process defects, and they often have a huge impact on the quality of products or services offered by the organization. Identifying and addressing them as soon as possible can help improve the organization’s output and consequently reduce customer complaints.
- Enhanced efficiency
Non-conformance management systems streamline the task of identifying, documenting, and addressing non-conformance incidents. Often, robust non-conformance management systems come as a suite alongside other quality management solutions which further eases decision-making by the quality management team. Ultimately, the organization’s entire quality management system becomes more efficient, and non-conformance incidents can be treated immediately.
- Cost savings
Depending on when they’re identified, non-conformances can lead to reworks, product recalls, regulatory fines, and in extreme situations, lawsuits. Implementing a robust non-conformance management system facilitates early detection of non-conformances and prevents future occurrences. Consequently, the financial impact of non-conformances will be minimized.
- Increased compliance
As mentioned earlier, organizations in certain industries such as pharma and life sciences, have to adhere to strict regulatory standards. Without a robust non-conformance management system that facilitates immediate documentation of incidents, such companies are likely to run afoul of these regulatory standards. This can expose them to fines or even stricter punishments.
- Increased customer satisfaction
When organizations promptly address non-compliance, they’re inadvertently improving the quality of their products and services. Consequently, there’ll be a ripple effect on the customer base as they’ll be more satisfied with the company’s offerings.
Types Of Non-Conformances
Auditors typically classify non-conformances as either major or minor, depending on the nature of the problem and how it will be addressed. However, it’s vital to note that the classification is usually for internal action as regulatory bodies do not discriminate between major and minor non-conformances. Below is a summary of the two types of non-conformances:
- Minor Non-Conformance
Minor non-conformances are easy to detect and do not occur frequently. Importantly, they do not have a significant impact on customer health or the organization’s reputation. Some common examples of minor non-conformances include:
– An unsigned or missing document
– Using an instrument past its date of calibration
– Unauthorized personnel making changes to a document
Although minor non-conformances may not seem very significant at face value, it’s still vital to address them as quickly as possible. For one, unaddressed minor non-conformances can lead to major incidents. Plus, as mentioned earlier, regulatory bodies do not distinguish minor or major non-conformances. - Major Non-Conformance
A major non-conformance is not easy to detect and it’s more likely to recur often. Crucially, it can have a significant impact on the customers’ health and the organization’s reputation if not nipped quickly. Some common examples of major non-conformances include:
– Shipping out untested products
– Multiple personnel making unauthorized changes
– Multiple missing documents
The importance of addressing major non-conformances quickly and effectively cannot be overstated. Leaving them to fester poses significant internal and external threats to the organization. For example, unaddressed non-conformances have been traced to increases in product failures, product recall frequency, and declined customer satisfaction. This negatively impacts the safety of consumers as well as the organization’s reputation.
What are Some Essential Aspects of A Non-Conformance Management System?
The overall aim of any non-conformance management system is to facilitate early detection, accurate documentation, and timely processing of non-conformances. This can only be achieved if the right foundation is in place and all team members are aware of their role in detecting and reporting non-conformances. Below is a highlight of the essential aspects of any non-conformance management system:
- Design
A non-conformance management system must be custom-made for the organization. For example, the processes involved in managing non-conformances in a small organization may vary from that of a large organization, the same way a service-based system would differ from a product-based system. The design process should garner inputs from the experts within your organization, and the output should be easily understood by all the parties involved.
The design should also state the criteria for grouping non-conformances into major or minor so that appropriate action can be taken. Furthermore, all incidents should be grouped accordingly, and there should be quality record data templates that will allow for tracing the source of the non-conformance.
- Documentation
All non-conformance systems must have a Standard Operating Procedure for documentation. The system should have a process flow chart that shows each person’s role in the documentation process and personnel should be trained accordingly. Importantly, documentation should be timely and detailed so that auditors can have all the information required to categorize the issue and take appropriate actions. Highly detailed reports also ensure data integrity and, consequently facilitate accurate data analysis and insights.
- Implementation
Effective implementation is a critical aspect of any non-conformance management system, and this can only be achieved if all team members have clearly defined roles and there’s cooperation and continuous monitoring. There should be a process owner who’ll be in charge of the entire implementation process and would be held accountable if lapses occur. The process owner would monitor other employees involved in the system to ensure they have a clear understanding of their roles. In addition, there should be regular meetings between team members to discuss the status of non-conformance incidents.
- Audit
Subjecting your non-conformance management to regular audits by specialists who are non-team members helps strengthen the system. Such specialists can identify obvious or potential weaknesses in the organization’s standard operating procedures and suggest possible strategies for improving the non-conformance guidelines or better still, preventing non-conformances. Subsequently, implementing the strategies would reduce the negative impact of non-conformances on the organization and its customers. Also, audits are necessary to ensure continual compliance with the non-conformance guidelines and assess the efficiency of the process.
Importance of Software in Non-Conformance Management
Like most other business processes, handling non-conformances used to be chiefly paper-based. However, physical documentation of non-conformances comes with many downsides. Some of them include:
- Longer retrieval times: Retrieving past non-conformance audit reports becomes more difficult as the years roll by if the organization is operating a paper-based system. Moreover, there’s a risk of damaged or missing files, and this could negatively impact future decision-making.
- Data disconnect: More often than not, a paper-based system leads to disjointed data collection. Even when related non-conformance incidents occur, it may be difficult to connect the dots if the organization still relies on physical documentation. For example, a series of non-conformance incidents may be traceable to a single supplier but the auditors may have difficulty finding the link due to disparate data.
- Policy adherence concerns: Paper-based systems are typically fraught with certain policy adherence issues if there’s no strict monitoring. For example, some essential information about the incident may not be missing in the file or the incident may be left unaddressed. If there’s no proper check in place, these issues may not be detected until much later.
The right non-conformance management software seamlessly addresses these problems while offering many other benefits. Some of the benefits include:
- Identifying defects and taking action: Non-conformance management software allows organizations to record and automatically track all identified non-conformance cases. With the right software, process owners can record all the pertinent information surrounding the defect, including the source, defect statement and code, occurrence date, date of reporting, corrective action taken, etc. Ultimately, taking the necessary corrective action becomes much easier with the right data. Plus, regulatory bodies may demand the information during non-conformance audits.
- Streamlining the quality management process: Most non-conformance management software now comes as a suite alongside other quality management solutions such as document version control, corrective/preventive action management, deviation management, etc. As such, the company’s entire quality management workflow is streamlined, and complying with regulatory stipulations becomes a lot easier.
- Root cause analysis: With the right software, organizations can easily identify the exact cause of non-conformances, especially if such incidents are linked to repeat occurrences. For example, if non-conformance is linked to raw materials from a particular supplier, the software can trace the link based on previous non-conformance data and alert the process owner. This allows the organization to take decisive action.
- Notifying the relevant personnel: Non-conformance software can bring the much-desired efficiency to non-conformance management by notifying the relevant personnel whenever a non-conformance is identified. This is particularly useful in large organizations where the process owner may not be able to directly supervise every aspect of the production and distribution process. Alerting relevant personnel ensures the necessary action is taken as quickly as possible, and there may even be follow-up alerts to further facilitate compliance.
- Reporting and analytics: The exhaustive data gathered by non-conformance management software gives room for generating detailed reports about the organization’s non-conformance process. Consequently, process owners can track the effectiveness of their non-conformance management process and identify ways to strengthen it.
What to look out for in non-conformance management software
There’s no over-emphasizing the importance of software to any non-conformance management system. However, with the proliferation of non-conformance management software options, it’s vital to carefully consider your options before settling for anyone. Apart from the benefits highlighted above, here are a few other features you should look out for when choosing non-conformance management software:
- Assign tasks to multiple team members: The right software should be able to assign different tasks to concerned team members. There should also be a feature that tracks the progress of these tasks to ensure compliance.
- Calculate non-conformance cost: Any credible non-conformance management solution should be capable of calculating the true cost of non-conformance incidents.
- Centralize non-conformance data: The software should be able to store the company’s entire non-conformance records in a secured and centralized system. This facilitates easy retrieval of records, either for regulatory or analytical purposes.
- Mobile friendly: The application should allow relevant personnel to access and launch non-conformance records anywhere and anytime.
- Connect with other quality management applications: The best non-conformance software comes as a suite that connects with other quality management applications. This connectivity ensures the organization’s quality control team is always on top of its game as it’ll have continual access to all relevant quality management data and assigned tasks.
Conclusion
Non-conformance management is an essential aspect of quality management. Organizations with a robust non-conformance management system are better placed to offer quality products and services, maintain compliance guidelines, and make fewer errors that can lead to costly reworks or product recalls. In recent times, non-conformance management software has become the backbone of these systems. Investing in the right software helps streamline and automate the non-conformance management process while giving the quality management team unlimited access to all essential information and tracking actions.